


The horticultural industry continues to struggle with labor issues both in terms of cost (minimum wage and associated benefit increases) and availability (immigration reform; lack of skilled workers). Moreover, it has been difficult to encourage the younger generation entering their collegiate years to consider a career in the horticultural industry.
Therefore, it is not surprising that many nurseries are pivoting towards using automated equipment as a viable, scalable and cost-effective solution to current labor shortages.
Data collected by the American Society for Horticulture Science concludes that, “Greater than 40% of production costs are labor costs, totaling nearly $40 billion per year in the U.S. alone.”
Beyond alleviating some of the issues surrounding labor shortages, automated equipment at nurseries also increases overall proficiencies and reduces the amount of human error in the process.
But it is important to understand the pros and cons when it comes to automated equipment which has a high upfront cost, requires some additional oversight and inspection and, as it is a machine, can be finicky and plagued with issues if not utilized correctly.
Additionally, not all planting containers are created equal. If you are not using an automation-compatible container with your new state-of-the-art equipment, you run the risk of internal damage which may not be covered under the manufacturer’s warranty.

Automation-compatible growing containers
So what makes a growing container automation compatible?
An automation compatible container should have uniform spacing between the container rims when stacked and a defined round or square rim for automated de-stacking tools to grab for easy denesting. If there is not enough space for the automated flange, lugs or spool type strippers to grab the rim, you run the risk of pulling multiple containers into the machine all at once, with the loose containers becoming jammed in the equipment.
If you are planning on using automated handling equipment such as fork systems, you will want to make sure that the rim protrudes far enough from the container body so it can securely rest on the tines. Many fork systems typically recommend rims that protrude 3/8 to a 1/2 inch.
Additionally, a sturdy side wall construction is necessary in order to withstand the force of the automated equipment (especially helpful on conveyers). If the walls are too thin, they can often crush under the machine’s pressure.
Blow mold containers, while a popular choice for nursery growers in the field, are not ideal for use with automated equipment. Their thin, side wall construction and ribbing causes challenges with denesting equipment and conveyor tables, and the absence of a pronounced rim prevents them from being used with fork systems.
Injection containers on the other hand are a solid choice for automated equipment. Injection containers are manufactured with thick side walls and heavy bottom construction to withstand the force of automated machinery, and sturdy, protruding rims provide excellent support for automated handling equipment, as well as seamless denesting.
APPROVED_fmt.png)
For growers familiar with thermoform containers, they do pose some limitations you must consider before implementing. While they are promoted as automation friendly, thermoform containers are not an ideal choice for dispensing equipment based on denesting challenges, but can be used with fork systems if the rims protrude sufficiently.
It is important to remember that thermoform containers are traditionally lighter weight for a lower cost, which means they may not be able to endure the physical demands of some automated equipment (such as pruning, pot washing and top dress tasks).
Another thing to be aware of is the shift from de-stacking automation (mentioned above) to suction type pot destacking equipment. In this application, a small suction cup grabs the bottom of the pot directly in the center – dropping or flipping it into the corresponding tray (or conveyor system) as part of the production line. If your automated equipment has this new technology, it is important that the bottom center of the pot be completely flat, otherwise the machine will be unable to properly grab the container. This is important to remember when purchasing containers with “feet” designed for water mat and other unique irrigation practices as there may not always be enough surface area for the suction cup to grab on to.
Investing in automated equipment can be scary, but as long as you do your homework and make sure that your containers are in fact automation compatible, the benefits will be plentiful.
For specific questions surrounding automation compatible containers or for a sampling of containers to test at your growing operation, contact Rick Friedrich today at 216-339-2914 or email RFriedrich@hc-companies.com.
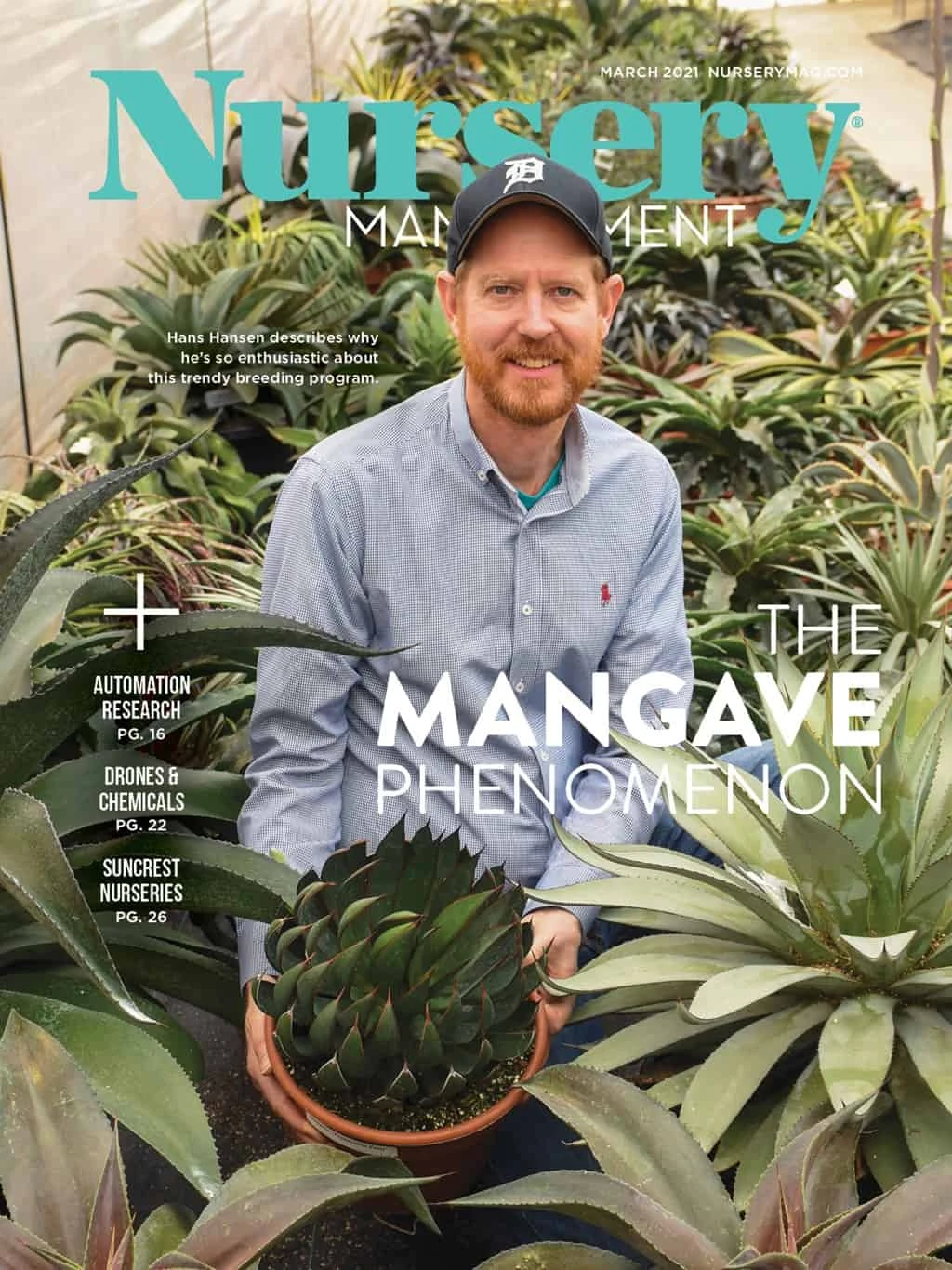
Explore the March 2021 Issue
Check out more from this issue and find your next story to read.
Latest from Nursery Management
- The Growth Industry Episode 3: Across the Pond with Neville Stein
- What's in a name?
- How impending tariffs and USDA layoffs impact the horticulture industry
- Shifting the urban environment
- These companies are utilizing plastic alternatives to reduce horticultural waste
- How to create a sustainable plant nursery
- Lamiastrum galeobdolon ‘Herman’s Pride’
- One of rarest plants on earth: Tahina spectabilis