Not only do growers need to think about which type of growing media is right for a particular plant, they must consider that plant’s application, as well.
SkyGarden is a division of Stancills Inc., a family owned and operated mining and manufacturing company located along the northern shores of the Chesapeake Bay. While SkyGarden has been creating custom mixes for green roofs for 15 years, Stancills has been blending soil for more than 80 years. The company produces custom equestrian footing, green roof planting media, soil mixes for engineers, horticulturists and landscape designers, infield and sports field mixes and other custom blends.
Chris Siciliano, director of sales for Stancills, says his customers appreciate the work that goes into a special blend. Typically, a customer will come to him with a specification – some idea what they want.
“Some growers know they want X percent coconut coir, X percent peat, X percent this type of lightweight aggregate or a type of sand,” Siciliano says. “We’ll put it together for you and make you a sample to see if it’s what you like. You can dial things in and out by percentage. Or if you want to add more perlite, let us know. We can meter all that in and make a custom mix. We’ll work with you to come up with what you’re looking for.”
Strong roots
The ability to easily increase or decrease percentages of certain ingredients is a popular feature with growers of green roof plants. But one of the biggest jobs growing media needs to do is improve the plant’s root system. If you want to ensure a stronger plant, the root system is the first place to look.
“In order to build really successful plants, you want a solid root system in there,” Siciliano says. “A lot of the materials in SkyGarden’s green roof media have a more arid material with a higher drainage content to it. Also, low organic content is important to SkyGarden’s succulent blend. It’s a delicate balance between giving the plant enough or too much – what may help a plant in the short term may not be the best choice for its long-term health. Some calculated adversity is useful to help the plant’s root system to establish. They’re succulents – they can take it.
“These plants will survive,” Siciliano says. “They are very tough plants. Give them a chance to let their roots really grow and reach and establish, so that when harsh conditions do come along, their roots are established, they’ll find the water they need easier than a plant that has been grown in say, compost, or a high compost mix, where the roots have gotten everything they need and so they aren’t establishing anymore.”
SkyGarden (and its parent company) is not a compost producer and not a lightweight aggregate producer.
So for the company, there is no advantage to using one type of material over another for growing media blends.
“We’re not pushing any one material; we’re making what’s best for the plants,” Siciliano says. “Because of that, our material tends to be more expensive, but it’s worth it because it’s the right stuff.”
Getting started
The business got its start making soil blends for golf courses. One particular client wanted all the different putting greens to have different blends, because they were located within different microclimates. Some were subject to high winds. Some were going to see more shade than others.
That was the beginning. And the Maryland-based soil scientists have been tweaking their media blends ever since.
Soon Stancills began constructing purpose-built equipment for blending media. The company continued to add capacity when green roofs were introduced, more than doubling the amount of blending that could be done.
“That’s when we started hammering out the precision blending aspect of it,” Siciliano says. “(We were) learning the controls of how best to proportion the materials to get it in the mix at a consistent rate.”
The bin blending system has several advantages, Siciliano says. First, it ensures you’re getting a quality mix.
“When you mix with a bucket loader, you can do it accurately, and it can be mixed, but there is a lot more opportunity for error,” Siciliano says. “We’ve eliminated as much of that as possible.”
On a bucket loader, one size speed does not equal another size. When you’re mixing the components for a media blend, one person might mix it more than another would. If a blend is not mixed thoroughly enough, you’re going to end up with pockets of really dry material and pockets of compost. So plants in one area of an installation are receiving too much organic, and others in another area of the installation are not getting enough.
“Every square foot of our material as it comes out is perfectly proportioned, goes through a passive blending system,” Siciliano says. “That means that what is made today, if a grower wants more of the same blend a year from now, it is going to come out as close as it possibly could be.”
Because SkyGarden has the entire process computerized, they are able to adjust on the fly.
“We can make one customer’s material for a job, call it in, just change the machine, it switches over, adjustments are all made, then we can make perfectly spec’d material for your company in the afternoon, then go back to making our stuff. Then we can make ball diamond mix the next day. It really reduces that margin of error.”
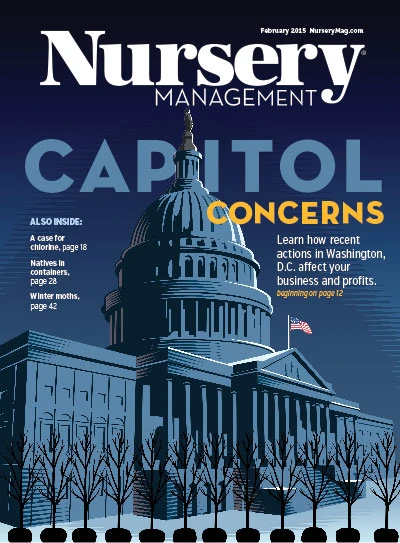
Explore the February 2015 Issue
Check out more from this issue and find your next story to read.
Latest from Nursery Management
- March 2025 issue recap
- Gratitude as a marketing strategy
- Leading Women of Horticulture: Katie Dubow, Garden Media Group, and Aubry Field, Lizzy Blossom
- Leading Women of Horticulture: Arden Pontasch, North Creek Nurseries
- Super Charged Moon Juice from Moon Valley Nurseries now available nationally
- 2025 Proven Winners Horticulture Scholarship applications now open
- Leading Women of Horticulture: Anna Ball, Ball Hort, and Terri McEnaney, Bailey Nurseries
- Leading Women of Horticulture: Crystal Cady and Elizabeth Brentano