

Once considered by many to be only a waste product (by-product) of the pulp and lumber industries, bark is now a highly valued commodity with increased usage and demand. Whether it is Douglas fir on the west coast, spruce or various pine species in New England and throughout Canada, or in the southeast where loblolly, longleaf and slash pines dominate the forests, the bark removed from these trees after harvest is increasingly in high demand.
Bark has been used as a fuel source in various industries for many years, it has beautified our landscapes as a decorative mulch, and it has been the backbone of the ornamental horticulture production industry as the number one substrate material for several decades. All of those uses remain true today, with one exception. The volume now needed to supply the growing demand of the ever-evolving and rapidly growing horticultural market is unprecedented. Let’s take a quick look at some of the drivers behind the increased interest and utilization of these materials in the horticultural market.
Bark that is removed from harvested trees (de-barking) at lumberyards is contracted to bark processors, those companies that will turn the bark into horticultural products, wither mulches or substrate materials. These bark suppliers then process the raw (fresh) bark in a variety of ways, and most often age it for some length of time, before selling the final product(s) to nursery growers or growing media manufacturers who will use it in the formulation of other growing mixes. The raw bark that arrives from the lumberyards is dumped (quiet literally!) on site (Figure 1) and is either processed in some way immediately or is stockpiled for future use. The quality of the raw bark varies based on the age of the tree it was harvested from, the species of tree, the geographical region the trees were grown, and even the time of the year that the trees were harvested. This raw bark can vary in size, thickness and amount of white wood and stringy inner bark contained in it, as shown in Figure 1D. Due to the coarseness of fresh bark (large particle sizes), it can be stored in piles for weeks or even many months before being further processed (hammer milled most commonly).
Whether processed immediately upon arrival to the bark processors facility, or if inventoried and processed after some period of time, the end goal is to create unique and specific particle sizes that can then be used in the formulation of different substrate products (Figure 2). Particle sizes can be created to be uniformly large, chunky and rounded for something specific like substrates for orchid production, or it can be pulverized to make a substrate that is more similar in size and physical properties to peat or coconut coir (middle photo in Figure 2). That said, keep in mind that even if bark is processed to mimic the size and physical properties of peat or coir, it does not mean that the materials will function the same when used in substrates to grow plants. Substrate engineers can match the physical properties of different materials but they cannot replicate the chemical, biological or nutritional properties as easily.
The demand for bark substrates, like all other growing media components, has been off-the-charts since 2020 driven by the effects of the Plantdemic (otherwise known as the pandemic) where homeowners purchased plants and garden products at historical rates. This of course prompted plant producers, both greenhouse and nursery crops, to grow more plants therefore driving up the demand of bark and other substrates. Based on the most recent data and market reports, sales of plants in 2022 have been more varied and overall lower than the previous two to three years, but are still higher in many segments than pre-plantdemic.
An additional drain on bark supplies has been a result of the supply issues of other substrate materials, namely peat moss. The most abundantly used substrate material in soilless plant cultivation; peat has seen demand reach levels that have never before been encountered. Most all peat producers (companies) in Canada sold out of peat in 2020-2021 and as a result had to cancel orders, reduce product offerings, deny new customers and be very strategic in how to best extend and stretch their supplies. Similarly, coconut coir, the second most consumed organic substrate component globally, saw nightmarish shipping disruptions and other complications getting the products out of south Asia. As a result, more bark was often used to fill these voids in the supply chain, where possible. That often meant higher percentages of bark materials in retail garden products and in professional greenhouse mixes. Bark, being an aggregate in peat or coir-based mixes, was also used to fill the void of the perlite shortages, which also were severe across the country.




Transportation has also played a major role in the availability of bark products to some areas. Notably, the issue of trucking/trucker shortages across the continent has driven up shipping costs or severely delayed the delivery of products to growers. There has also been extreme challenges getting raw bark barged up the Mississippi River from Mississippi and surrounding states up north to bark processors/supplies in the Midwest who make bark substrates to supply markets in that region of the country. When bark could not get up the river, the suppliers upstream had to look to other alternatives to stretch or supplement their traditional bark substrates in order to provide their growers with the substrate volumes they needed. Of course, for growers in some parts of the south and Pacific Northwest who are in close proximity to the major bark producers, these shortages or delivery delays were not as problematic.
One of the solutions to the bark, peat and coir supply issues has been an increase use of wood products in substrates across the U.S. Admittedly, more of a solution to the supply issues and costs of peat moss, wood fibers and other wood products saw increased use in both retail hobby market and profession market products. Wood materials, including in some cases hardwood bark and wood, which is very uncommon, were used in place of traditional pine bark to stretch supplies and supply customers. The most common practice I have seen and heard about is the use of hammer milled or other engineered wood products with bark either to stretch bark supplies when needed or to create new, possibly cheaper, mixes. There are several commercial wood products on the substrate market today, one of which that is made by some growers themselves is hammer milled pine tree substrate (Figure 3). As we learn more about how to use fresh (non-composted) white wood materials in our mixes, we are building more confidence in how to be successful with these new mixes. Inclusion rates of under 40% are still most common (both in peat and bark mixes) but some growers are learning how to grow with them and are pushing those percentages higher as they are seeing economic benefits of doing so.
The last major potential competitor, and driver of product demand in the future, is the explosive growth of soft fruit production in indoor or outdoor soilless growing systems. Still considered “a trend” by some, I view the future transition of more traditionally field-grown berry crops to container production to be one of the greatest users of bark-based substrates in the not-to-distant future. Blueberries are the crop most quickly transitioning (globally) to outdoor production in soilless substrates but not far behind are bramble crops, citrus, figs and maybe even large acreage of fresh market grapes on the east coast. Also, let us not forget strawberries! If the transition to soilless production of soft fruit in Mexico, Peru and other parts of the world are any indication, I predict hundreds of acres of berries in outdoor nursery production systems (just in the Southeast) in the next few years. I also predict pine bark will be a major source of the substrates needed for these crops. Will this compete directly with ornamental nursery producers? Can the bark suppliers meet the growing demand of both industries? Time will tell.
What does all of this mean? For starters, growers have had to be flexible, willing to change some growing practices, and be resilient in the face of these industry-wide challenges. Secondly, substrate manufactures have learned new ways to use new materials to create substrates. This will likely be the “new norm” in many situations and whether these changes in substrate composition (and price) remain in place or go back to being more like they used to be a few years ago is yet to be seen. What I think is pretty certain, is that more investigations and research into novel substrate materials is only going to increase so that we are better prepared as an industry to meet supply and demand challenges of the future, but also to be more conscience of substrate costs, renewability and sustainability. Final thought on this matter… keep ordering your substrates earlier than you used to, build relationships with you chosen substrate supplier and be willing to adapt to new products and production practices if and when needed.
Get curated news on YOUR industry.
Enter your email to receive our newsletters.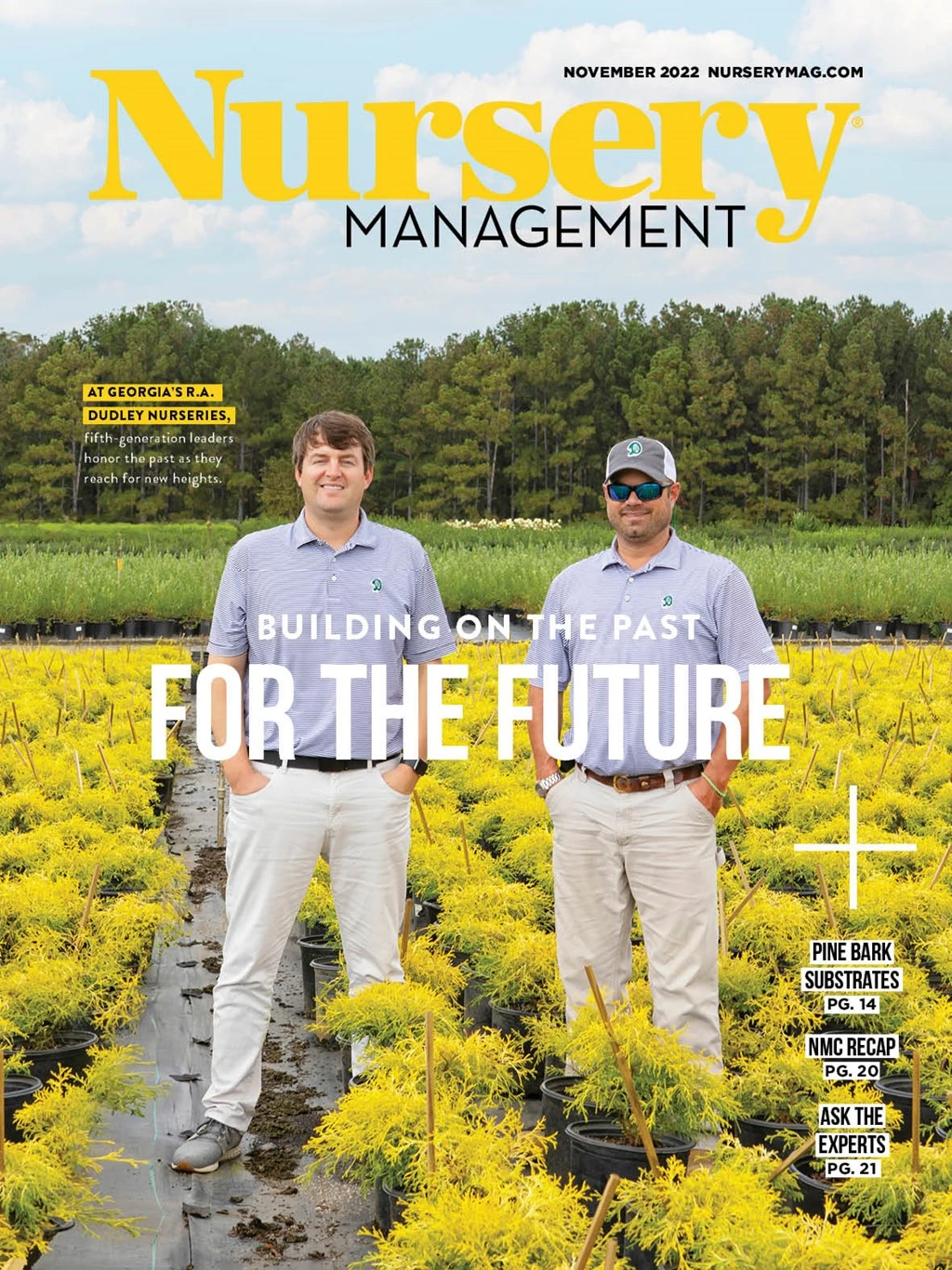
Explore the November 2022 Issue
Check out more from this issue and find your next story to read.
Latest from Nursery Management
- NewGen Boxwood added to Proven Winners ColorChoice line
- Terra Nova releases new echinacea variety, 'Fringe Festival'
- American Horticultural Society names winners of 2025 AHS Book Awards
- Nufarm announces unified brand
- American Horticultural Society announces winners of 2025 Great American Gardeners Awards
- Shifting the urban environment
- The Growth Industry Episode 3: Across the Pond with Neville Stein
- What's in a name?