
Photo: Gerry Spinelli
Spray stake technology is common in nursery production systems, yet their distribution uniformity has been poorly studied. Recent innovations have the potential to increase distribution uniformity, but may be cost prohibitive. We analyzed the distribution uniformity of two brands of spray-stakes with and without pressure compensating emitters. We then conducted a cost comparison of switching from non-pressure compensating emitters to pressure compensating emitters. The average distribution uniformity measured was: 0.85 for one brand of non-pressure compensating spray stakes, 0.82 for another brand of non-pressure compensating spray stakes, 0.95 for pressure compensating spray stakes of the first brand, and 0.95 for pressure compensating spray stakes of the second brand. While pressure compensating emitters do increase distribution uniformity, it would take 4-6 years based on water savings for the investment in pressure compensating emitters to break even, based on Southern California water prices.
Spray-stakes for nursery production
Spray-stakes have been a staple of the nursery industry for decades. The innovator in the field of spray-stakes has been Roberts Irrigation products from San Marcos that started producing the famous Spot Spitter in the 1970’s. These are one of the first examples of localized irrigation (aka micro-irrigation) that allows water to be applied directly to the root zone, as opposed to overhead sprinkler systems that apply water to the whole field. Localized irrigation technologies have great potential for water and nutrient conservation, particularly in containerized systems where the water that falls between containers is inevitably lost and potentially generates water and nutrient runoff (Abdi et al, 2021; Bilderback, 2002). This makes spray stakes particularly well suited for large containers and thus they are mostly used in tree, shrub and palm tree production (Fulcher et al. 2016), however, their distribution uniformity is anecdotally reported to be lower than in drip systems.
Various irrigation companies produce spray stakes. These are hard plastic stakes that are inserted into the container substrate and on the other side plug into a 1/8 inch spaghetti tubing. The function of the stake is to hold the tubing over the container while it sprays downwards towards the substrate. A slot in the plastic pin that plugs into the tubing creates an opening for water to come out and acts as a spray nozzle. Different colors are associated with different slot sizes and spray angles, creating different flowrates. The side of the stake that sticks into the substrate also has a 1/8 inch size pin, but without the slot, used to plug the tubing when the container is harvested from the field. This feature allows workers to “turn on and off” spray stakes when they are not in operation preventing the production of irrigation runoff. The simplicity of spray-stake technology and operation is the basis for its success. Spray stakes operate at pressures between 15 and 25 psi. The configuration of the stake varies slightly depending on the manufacturer, but the fundamental working principle remains the same.


While spray stakes offer many advantages, the spray orifice lacks a tortuous path, making the flowrate more sensitive to pressure differences than drip emitters. There is also variability caused by the angle at which the spaghetti has been cut, the depth of insertion of the stake into the spaghetti, etc., that can affect the volume of water applied by each spray stake. There are also reports of plugging issues with the spray slot of low flowrate models. Other challenges are associated with the amount of area covered by the stake spray pattern within the container, with the risk of preferential flow through the substrate when the flowrate is high, and/or the covered area is small. Lamack and Niemiera (1993) measured application efficiency in a brand of spray stakes and showed that higher efficiency was associated with lower application rates and with intermittent irrigations.
Recently, manufacturers have commercialized spray-stakes equipped with an assembly of tubing and a pressure compensating (PC) emitter that plugs into the main supply hose. The addition of a pressure compensating emitter produces a flowrate that is independent of the upstream pressure. This new solution, although more expensive, should produce more uniform volumes of water being applied to each plant container.
In this study we evaluated two brands of spray-stakes without pressure compensating emitters and two models of the same brands with pressure compensating emitters, measuring distribution uniformity of the low quarter (Clemmens and Solomon, 1997). Based on the collected data, we also attempted a cost comparison using current water prices in San Diego County.


Distribution uniformity measurements
In this study, we tested one brand (Brand A) of spray stakes with and without pressure compensation (PC) and another (Brand B) with and without pressure compensation. The Brand A model tested had a nominal flowrate of 7.2 gph at 25 psi. This was tested both with and without pressure compensating emitter. The non-pressure compensating Brand B spray-stake tested had a nominal flowrate of 7 gph at 20 psi and with an operating pressure of 15-20 psi. The pressure compensating Brand B spray stake tested had a flowrate of 6.6 gph, with a double spray pattern and a standard stake mounting option. Both brands spray-stakes used the same pressure compensating emitter with a “shutoff valve” feature that turns off the emitter at pressures lower than 2 psi to avoid drainage of the main hose upon shut off.
During the tests, pressure compensating emitters were operating at a pressure between 25 and 55 psi, (the recommended operating pressure on the Brand B spray stakes brochure is 22 to 55 psi and on the Brand A website is 20 to 60 psi). During the tests, we installed a Senninger 25-psi pressure regulator upstream of the non-pressure compensating spray stakes to lower the pressure to 25 psi. For further testing we swapped the pressure regulator with a 20-psi one. The measured pressure after the pressure regulator was always in accordance with the nominal pressure regulator pressure, 25 or 20 psi. We installed a 150-mesh filter at the beginning of the supply hose as recommended by the spray stakes manufacturers.
We measured distribution uniformity and flowrate by collecting water in 25 one gallon buckets per each spray stake tested for 2 minutes. We then measured the volume of water in each bucket with a graduated cylinder. Based on these volumes, we calculated the distribution uniformity of the low quarter. Flowrates were calculated by dividing the average volume collected in the buckets by the run time.
The distribution uniformity measured was on average 0.85 for the non-pressure compensating Brand B and 0.82 for the non-pressure compensating Brand A (Table 1). It was 0.95 for the PC Brand B and 0.95 for the PC Brand A. The measured flowrate at 20 psi was 7.9 gph for the non-PC Brand B and 7.1 gph for the non-PC Brand A; the flowrate at 25 psi was 8.8 gph for the non-PC Brand B and 7.6 gph for the non-PC Brand A. These values are higher than reported by the manufacturer, the Brand B non-PC nominal flowrate is 6.9 gph at 20 psi and the Brand A non-PC nominal flowrate is 6.6 gph at 20 psi and 7.2 gph at 25 psi. The observed flowrate for the PC Brand B was 6.5 gph, slightly lower than 6.6 gph reported by the manufacturer; and 6.1 gph on average for the for the PC Brand A. It is unclear from the manufacturer brochure what is the nominal flowrate for PC Brand A.
The observed distribution uniformity is good for non-PC spray stakes and excellent for PC spray stakes (Table 1, Figure 2). As a reference, in overhead sprinkler systems, a distribution uniformity of 0.75 is considered a good performance. Conversely, in a well-maintained drip system, distribution uniformities in the range of 0.9 to 0.95 are to be expected (Burt and Styles, 2011). In other words, non-PC spray stakes are a substantial improvement over overhead sprinklers, but their distribution uniformity is lower than that of drip irrigation. On the other hand, the distribution uniformity of PC spray stakes match that of drip irrigation, and the observed distribution uniformity in PC spray stakes is as high as the authors have ever measured. The distribution uniformity observed did not vary much from brand to brand, but did vary between PC and non-PC spray stakes. The pressure compensating feature worked as expected for both brands, resulting in essentially the same flowrate in a wide range of pressures (Figure 3). Conversely, the non-pressure compensating spray stakes showed higher flowrate at 25 psi than at 20 psi as expected.

Is switching to PC worth it?
Let’s say a nurseryman in Escondido irrigates a 10,000 square-foot block of five-gallon containers (10-inch diameter) spaced 20 inches center to center. Each container occupies a space of 20 inches x 20 inches = 400 square inches = 2.78 square feet, so there are (10,000/2.78) = 3,597 containers in the block. Let’s say that the nursery grows year-round, and uses CIMIS (cimis.water.ca.gov or similar local weather-based service that provides reference evapotranspiration data) to decide how much to irrigate, trying to apply reference evapotranspiration. The average yearly reference evapotranspiration in Escondido is 53.7 inch (obtained from CIMIS). Since 10,000 square feet is equal to 0.23 acres, the yearly volume used by plants is (0.23 x 53.7) = 12 AcIn = 1 AcFt. In San Diego County, one AcFt of municipal water costs about $2,500.
To apply 12 AcIn of water with a distribution uniformity of 0.82 (non-PC Brand A) one needs to apply 12/0.82 = 14.6 AcIn. However, if applying irrigation with a distribution uniformity of 0.95 (PC Brand A), one only needs to apply 12.6 AcIn. The improvement in distribution uniformity saves the grower 2 AcIn (0.16 AcFt) which amounts to $416.
If the grower switches from non-PC Brand B spray stakes to PC Brand A, DU will improve from 0.85 to 0.95, saving the grower 1.5 AcIn (14.1 – 12.6 AcIn) or $310.
Now let’s look at the cost of spray stakes. A bundle of 100 Brand A PC including the 36-inch spaghetti assembly costs $74, while 100 non-PC Brand A, including a spaghetti tubing of the same length costs $27, that’s $0.47 cheaper than the PC version per unit. So, the grower spends $0.47 x 3,597 = $1,690 more to install pressure compensating Brand A in a 10,000 square foot block. The savings in water savings will pay off the initial spray stake investment in $1,690/$416 = 4 years.
Brand B non-PC spray stakes cost $0.20, while the PC assembly costs 0.88. Accounting for $0.10 for the spaghetti tubing, we get to $0.58 difference. The additional cost for the grower is $0.58 x 3,597 = $2086 and the investment pays off in $2086/$310 = 6.73 years.

Bottom line
In conclusion, our study found that pressure-compensated spray stakes substantially improve distribution uniformity and result in water savings that can lead to better compliance with water quality regulations. However, the current cost of this technology can be cost prohibitive in the short-run for a commercial operation compared to non-pressure compensating spray stakes. The estimated savings resulting from water savings alone may not justify a switch to PC spray stakes, even in areas like San Diego County where the cost of water is extremely high.
Abdi, Damon E., James S. Owen, Julie C. Brindley, Anna Birnbaum, Bert M. Cregg, and R. Thomas Fernandez. “Irrigation Return Flow and Nutrient Movement Mitigation by Irrigation Method for Container Plant Production.” IRRIGATION SCIENCE 39, no. 5 (September 2021): 567–85. https://doi.org/10.1007/s00271-021-00727-1.
Bilderback, Ted E. “Water Management Is Key in Reducing Nutrient Runoff from Container Nurseries.” HortTechnology Horttech 12, no. 4 (2002): 541–44. https://doi.org/10.21273/HORTTECH.12.4.541.
Burt, C., S.W. Styles, San Luis Obispo. Irrigation Training California Polytechnic State University, Research Center, Irrigation Training & Research Center (ITCR), Bioresource, and Agricultural Engineering Departament (BRAE). Drip and Micro Irrigation Design and Management: For Trees, Vines, and Field Crops. Irrigation Training & Research Center, 2016. https://books.google.com/books?id=s2dqjwEACAAJ.
California Department of Water Resources. n.d. “California Irrigation Management Information System, CIMIS.” Accessed July 30, 2023. https://cimis.water.ca.gov/.
Clemmens, A. J., and K. H. Solomon. “Estimation of Global Irrigation Distribution Uniformity.” Journal of Irrigation and Drainage Engineering 123, no. 6 (1997): 454–61. https://doi.org/10.1061/(ASCE)0733-9437(1997)123:6(454).
Fulcher, Amy, Anthony V. LeBude, James S. Owen, Sarah A. White, and Richard C. Beeson. “The Next Ten Years: Strategic Vision of Water Resources for Nursery Producers.” HortTechnology Horttech 26, no. 2 (2016): 121–32. https://doi.org/10.21273/HORTTECH.26.2.121.
Lamack, Wf, And Ax Niemiera. “Application Method Affects Water Application Efficiency Of Spray Stake-Irrigated Containers.” Hortscience 28, No. 6 (June 1993): 625–27. https://doi.org/10.21273/hortsci.28.6.625.
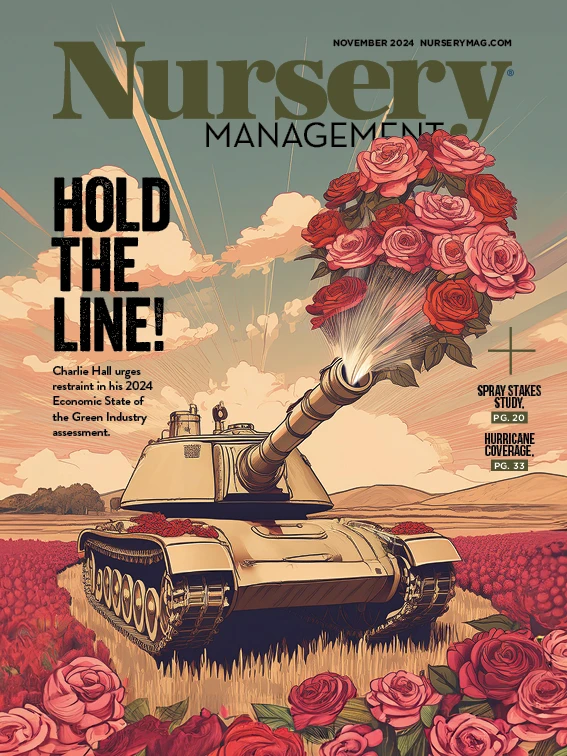
Explore the November 2024 Issue
Check out more from this issue and find your next story to read.
Latest from Nursery Management
- The Growth Industry Episode 3: Across the Pond with Neville Stein
- Trends: Proven Winners 2025 perennial survey shows strong demand
- Online registration opens for the 2025 Farwest Show
- Sustainabloom launches Wholesale Nickel Program to support floriculture sustainability
- Plant breeding as an art
- Society of American Florists accepting entries for 2025 Marketer of the Year Contest
- American Horticultural Society welcomes five new board members
- Get to know Christopher Brown Jr. of Lancaster Farms