
Typically, the first step in irrigation water treatment is physical removal of larger particles such as sediment, substrate material and organic matter, which was discussed in the first article of this series (August 2017). But rapid sand, mesh filters, etc. are not able to remove agrichemicals such as plant growth regulators and herbicides (see article in September 2017 issue) or biological contaminants such as Pythium, Phytophthora, and other plant diseases. Chemical disinfection is the fastest and most effective way to ensure removal of plant disease organisms from irrigation water.
Pretreating water is very important, particularly for effective disease control. Think about the extra stuff in your water (e.g., substrate debris and plant litter) and relate that to what happens when too many irrigation valves are open in your fields or container beds. When too many valves are open, the pressure drops, and none of the fields or beds are being irrigated correctly. Whether you are injecting a sanitizer or using UV light, the same holds true. The more “stuff” you have in the water, the less effective your sanitizer will be. It is possible for the sanitizer to be used up (consumed) before all the disease organisms in your water are killed. Chemical treatment efficacy declines if high levels of organic matter are present in water, making it necessary to increase the concentrations of chemicals needed to treat the same volume of water.
Chlorination
Chlorination is the most commonly used chemical treatment for ornamental production, due to its relatively low cost, availability, high efficacy, and relative safety. Chlorine can be used either as a solid (calcium hypochlorite), liquid (sodium hypochlorite or hypochlorous acid), or gas (chlorine). It is also possible to generate it on site through a process called electrolysis. The major concern with any type of chlorine system is the additional safety precautions that are required for its use, which vary by type of chlorine. Extensive discussions related to efficacy, dose, costs and benefits, and timing of chlorine injection are available.
It is recommended that there be 0.5 to 2 ppm of free chlorine at the sprinkler head to ensure adequate sanitation. Free chlorine levels should be checked at least monthly (preferably weekly) during crop production, as changes in water quality and the amount of organic matter in treated water impact the chlorine residual that will exit the sprinkler head. Always check free chlorine levels at the sprinkler furthest from the injector to ensure adequate sanitation throughout the system. Controlling water pH is also very important. When the pH is below 7.5, Hypochlorous acid (HOCl), the most potent sanitizing form of dissolved chlorine, will be present. At pH above 7.5, the hypochlorite form is present and is a much weaker sanitizer. If the pH of your water is ever over 7.5, acid injection into irrigation water is recommended prior to or with chlorine injection to increase chlorine efficacy. Many operations use chlorine for disinfection because of its cost effectiveness and relative ease of use.

Ozonation
Ozone (O3) is a strong oxidizer that disinfects by creating a reduction-oxidation reaction in the membrane of disease organisms and other organic materials. An ozone production system (corona discharge or plasma discharge units) uses electricity to split oxygen (O2) molecules to form ozone. Once formed, ozone breaks down into peroxides and other oxygen radicals that provide additional disinfection. No additional inputs are required, and no persistent by-products are produced. Ozone and its by-products degrade quickly in water, so direct testing is difficult, but in-line monitors that also control injection concentration are typically used for these types of systems.
Ozone efficacy is reduced in the presence of organic matter, high pH, and/or high concentrations of nitrite, manganese, iron, or bicarbonate. Knowing your water chemistry is critical for this type of system. Contact times of 2-30 minutes have been shown to control Phytophthora and Fusarium at a concentration of 1.8 ppm. Ideally, ozone would be injected into a storage tank, since longer contact times are more effective, a one-hour contact time was found to kill 99 percent of bacteria and fungi. Although operating costs are mainly for the electricity to run the system, installation costs are among the highest for any type of sanitation. Adequate ventilation and other fail-safes are also required for human safety.
Peroxides
Peroxides, like ozone, also create reduction-oxidation reactions to destroy plant disease organisms. Peroxides include hydrogen peroxide (H2O2) and peracetic/peroxyacetic acid, which form reactive oxygen (O2) molecules when added to water. Peroxides can also be used in conjunction with other treatments, such as ozone and UV, to increase their effectiveness. Peroxides are not generated on-site, and the chemical must therefore be purchased on an ongoing basis. Peroxides and other oxidants are corrosive, so any pipes and structures where this water is applied should be corrosion resistant. It is relatively easy to measure the concentration of hydrogen peroxide in an irrigation system using inexpensive test strips.
since longer contact times are more effective, a one-hour contact time was found to kill 99% of bacteria and fungi.


Copper and silver ionization
Copper or silver ionization systems release copper or silver ions that bind to proteins in any organism in the water, disrupting the protein structure and killing the organism. This type of system can help control biofilm growth in irrigation pipes and lines, as well as plant diseases. Once installed, ionization systems are often low maintenance and cost effective. Copper and silver could be considered pollutants of local waterways if present in runoff leaving the operation in sufficient concentrations. The EPA safe drinking water standard is 1.3 ppm for copper and 0.1 ppm for silver. Concentrations of 0.28-4.0 ppm of copper and 0.07-0.5 ppm of silver are effective for sanitation. Phytotoxicity can occur at concentrations of copper ranging from 0.19-1.05 ppm. To minimize potential for non-target crop damage, phytotoxicity tests should be performed on a small group of plants prior to use of water sanitized via copper or silver ionization.

Ultraviolet light
Ultraviolet light is an in-line treatment that uses UV-C radiation wavelengths (240 to 280 nm) to kill pathogens and micro-organisms. At 254 nm, the DNA and RNA of a micro-organism is altered, destroying it. High- or low-pressure UV lamps are typically used, with high-pressure lamps converting 10 percent of the power consumed to UV-C radiation compared with low-pressure lamps, which convert 40 percent of the power consumed to UV-C radiation. Sanitation efficacy depends upon exposure duration and intensity. Bacteria can be destroyed with as little as 3.5 to 26.5 mJ/cm2, while viral contaminants are destroyed with a UV-C dose of 100 to 277 mJ/cm2. Propagules (spores, zoospores, conidia) of fungal organisms (Alternaria, Colletotrichum, Fusarium) and oomycetes (Phytophthora and Pythium) that can infect plants are destroyed with UV-C doses from 10 to 70 mJ/cm2. Root infection by nematodes was prevented at 100 mJ/cm2, with organism death at 500 mJ/cm2.
Water clarity is the single most important factor regulating UV light water disinfestation efficacy. Organic matter and other particles (turbidity) in the water absorb, reflect, and/or diminish UV light. If using UV light to disinfest recycled water, it should be paired with a physical pre-filter treatment (e.g., sand, glass, disc, etc.) to remove turbidity, aiming for less than 2 NTUs (nephelometric turbidity units) to ensure adequate treatment of micro-organisms. A UV system must be sized for the maximum rate of water (gallons/minute) that is pumped to ensure adequate treatment. At lower flow rates, treatment effectiveness is improved. The biggest drawback of this system is that the high initial investment costs may limit adoption, even though maintenance costs are relatively low.
Although some of these technologies may seem less applicable in a nursery production setting, water quality or quantity concerns now or in the future might make these types of systems more appealing. Being able to recycle water within your operation while ensuring proper sanitation is required for disease management. We tend to take water availability and quality for granted, until the next drought or disease outbreak occurs. Planning for your operation’s future includes securing your water.
Get curated news on YOUR industry.
Enter your email to receive our newsletters.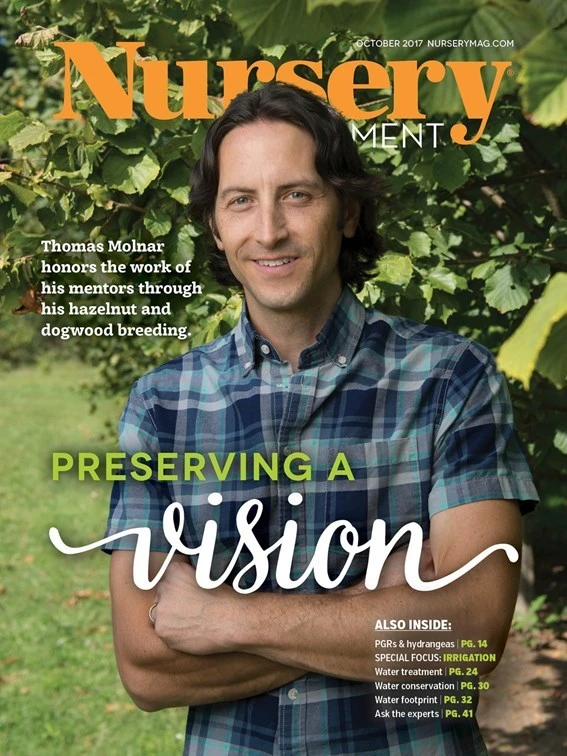
Explore the October 2017 Issue
Check out more from this issue and find your next story to read.
Latest from Nursery Management
- NewGen Boxwood added to Proven Winners ColorChoice line
- Terra Nova releases new echinacea variety, 'Fringe Festival'
- American Horticultural Society names winners of 2025 AHS Book Awards
- Nufarm announces unified brand
- American Horticultural Society announces winners of 2025 Great American Gardeners Awards
- Shifting the urban environment
- The Growth Industry Episode 3: Across the Pond with Neville Stein
- What's in a name?