

LEAP (Labor, Efficiency, Automation and Production) for Nursery Sustainability aims to better understand how automation can help address labor issues and contribute to nursery production capacity and the operation’s bottom line. Made up of representatives from the University of Tennessee Institute of Agriculture, in partnership with the University of Florida, N.C. State University, Oregon State University, Texas A&M University, and the USDA, and with guidance from an Advisory Board of industry professionals, the LEAP team is conducting research about nursery labor challenges and consideration of, and transition to, automation. Nursery Management editor Kelli Rodda caught up with LEAP team member Anthony LeBude, associate professor at N.C. State University, to learn more about the team’s progress and plans.
Nursery Management: How did LEAP come to fruition?
Anthony LeBude: Research and extension faculty from six universities and the USDA-ARS had been specializing on various facets of the LEAP components during their careers. Amy Fulcher at the University of Tennessee, Knoxville, provided the leadership that combined their strengths into a cohesive team capable of meeting the challenges identified by consulting with local and national nursery representatives, conducting one-on-one interviews, and holding video calls with our current Advisory Board. We are still building that team based on current feedback received from growers, our advisory board, and our current nationwide survey in circulation.
Editor’s note: Read on for more details about the survey.
NM: What are LEAP’s main goals?
AL: The long-term benefits include greater productivity and efficiency through reduced risk of relying on an uncertain labor force, thus aiding in not only preserving this $16.7 billion sector of U.S. agriculture but supporting its growth. Specifically, currently available and to-be-developed automation and related technologies will allow nurseries to survive with a limited labor force, while utilizing this research to ‘LEAP’ toward sustainability by improving the average profitability of nursery production due to reallocating labor to higher level tasks, achieving greater product reliability and uniformity, and through more compact production. Nurseries across a range of scales will be able to strategize key capital investments to increase capacity, deploy labor smartly, and create more efficient, safer work environments. The economic benefit experienced by nurseries will sustain rural communities and support nursery expansion.
NM: How does the LEAP team plan to achieve those goals?

AL: In this first planning stage, we are going to learn how other firms have prioritized, selected, and implemented various options available, then learn how those decisions have affected other aspects of nursery production with intended or unintended consequences, and finally identify what automation needs require new research and development.
NM: What actions have been taken to date?
AL: This work is supported by the Specialty Crops Research Initiative award number 2020-51181-32137 from the USDA National Institute of Food and Agriculture for the planning grant Labor, Efficiency, Automation, and Production (or LEAP) for Sustainability in Nursery Crops.
In support of this planning grant we continue to build our extensive advisory board that already includes every major nursery segment and operation size that grows ornamental plants in the nation.
In fall 2020, we scheduled a field day at Panoramic Farm in Marshville, North Carolina, and Decker Nursery in Groveport, Ohio, to invite growers to see firsthand adoption and retention of various strategies to improve labor and production using automation and other technologies. Because of the pandemic, we quickly pivoted to professionally producing videos on each nursery that included interviews, how-tos, and labor and automation vignettes highlighting successful innovations and their impact on nursery production.
Those videos are available on the LEAP website (www.nurseryleap.com). The videos allow viewers to learn the tips and tricks behind the philosophy and impact of adopting automation and related time-saving strategies or technologies from presidents or CEOs, production and special project managers, and nursery employees in several different positions.
We conducted professionally facilitated virtual listening sessions across every major production region in the U.S. with growers of ornamental crops. Our approach was to learn how they begin determining whether they should automate; what factors they use to evaluate automation options; what do they see as the greatest benefit of automation adoption; and what concerns do they have about the process.
Currently, LEAP is surveying growers across the U.S. to learn more about their experiences and expectations with various labor-saving techniques, automation, and other technologies to produce plants. Growers can complete the survey at https://tiny.utk.edu/Nursery-autom ation. It will remain open until April 11.
NM: What has the team learned so far?
AL: In our initial interviews, phone calls, and visits with growers across all segments and sizes of the nursery industry in the U.S., we found they are concerned about how labor challenges of availability and quality are going to affect their capacity to grow as a company. They are thinking deeply about their best options going forward to alleviate such dependence on an uncertain labor pool. We are still gathering information in our survey and we need everyone who is a wholesale, production nursery to complete it for us to have a comprehensive view going forward of growers’ visions, experiences, limitations, and perceptions of the adoption and retention of automation and other technologies as components of the solution to current labor challenges.
NM: Any surprises about what you’ve heard from growers regarding labor and automation?
AL: We knew growers relied on Cooperative Extension and evidence-based, unbiased information about plant production produced by state universities and the USDA-ARS in the past. We’ve been working with them for decades. We were pleasantly surprised, however, when growers all across the U.S. mentioned how those two organizations need to produce information they can use to identify where production changes can be made and help them evaluate choices by providing clear, credible information about the benefits and limitations of automation and technology. They were counting on us to help them make the transition. This project is going to meet those challenges and provide solutions they need to remain profitable in the future.
NM: What are the next steps in 2021 and beyond?
AL: Once we gather all our information and determine the pressure points that are applied to production by either adopting (or not adopting) and retaining labor saving techniques, automation or other technologies, we will present this information to our grower and allied industry advisory board to determine our best research and extension priorities to obtain solutions. We are going to submit a larger grant through USDA-NIFA this fall to obtain much needed support to enable growers of ornamental plants to remain profitable moving into the future.
NM: Do you think there are some misconceptions in terms of information related to automation and the nursery industry? If so, can you give some examples?
AL: One of the misconceptions we found has been that workers will be laid off when automation is adopted. We’ve found in several examples that the employees were reluctant at first to be ‘on board’ with change because of this misconception, and in some cases, may reject the technology because of this. After a while, however, employees realized how effective they could be at their position by utilizing the automation. In some cases, it promoted employees from lower-skilled positions to oversee parts of the production line, and in other cases employees offered suggestions to make it more effective. They realized how much work it takes off their shoulders, literally and figuratively, and are happy for the changes. Moreover, regular mundane tasks like pruning or potting are completed more quickly and allow available labor to be deployed throughout the nursery to add value to plants that wouldn’t necessarily receive such attention in the past this early in production, such as moving and spacing, fertilizing, or scouting.
For more: www.nurseryleap.com
Get curated news on YOUR industry.
Enter your email to receive our newsletters.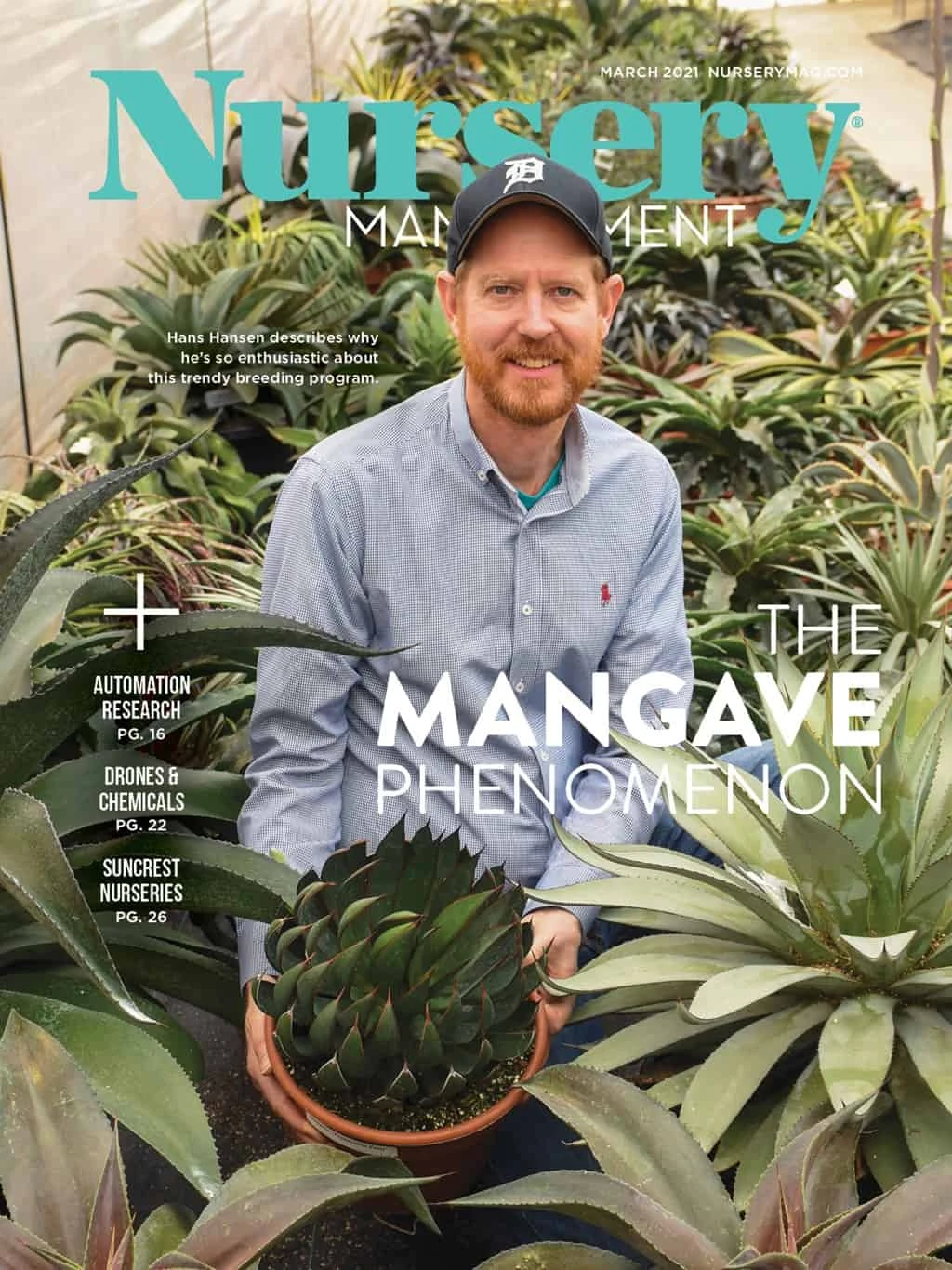
Explore the March 2021 Issue
Check out more from this issue and find your next story to read.
Latest from Nursery Management
- Trends: Proven Winners 2025 perennial survey shows strong demand
- Online registration opens for the 2025 Farwest Show
- Sustainabloom launches Wholesale Nickel Program to support floriculture sustainability
- Plant breeding as an art
- Society of American Florists accepting entries for 2025 Marketer of the Year Contest
- American Horticultural Society welcomes five new board members
- Get to know Christopher Brown Jr. of Lancaster Farms
- American Floral Endowment establishes Demaree Family Floriculture Advancement Fund